1. Abstract
This note depicts the use of a next generation Uncrewed Surface Vessel for the collection of bathymetric data in inland Canadian waters, via a partnership between IIC Technologies and XOCEAN performing services for the Department of Fisheries and Oceans’ Canadian Hydrographic Service (CHS). It will discuss how the operation was successful, lessons learned and how operations in a quasi-subarctic environment from October to the end of November 2020 are a suitable test of the equipment and operations for near Arctic conditions. In addition, it will discuss recommendations on how autonomous technology could greatly improve the efficiency and effectiveness of hydrographic operations in Arctic waters, where there is a need for modern hydrographic data.
2. Introduction
The need for high quality hydrospatial multidimensional data (Hains, 2020; Pang & Oei, 2020; Ponce, 2020 ; Ponce, 2019) in the world, and particularly in Arctic waters, has increased greatly in recent years. The retreating sea ice has caused a growing interest in maritime activities throughout the region (Maratos, 2011). As marine traffic increases through shipping, resource extraction and tourism, reliable and accurate aids to navigation are needed both for the safety of people and protection of the marine environment (Maratos 2011). With an Arctic Coastline of over 162,000km and a low population density, concern for Canada’s Arctic Sovereignty and identity has increased as more countries show interest in the region. Exercising sovereignty rights, defining boundaries with other Arctic states, and ensuring control of resources within Canada’s Economic Exclusion zone has become a priority of the Canadian Government (Government of Canada, 2017). Through Canada’s Oceans Protection Plan (OPP) there has been an increased investment in mapping of Canada’s Northern waters (Government of Canada, 2017). To expedite the mapping of Canada’s Northern waters, the CHS wanted to test the suitability of the latest autonomous survey technology in remote locations with challenging weather conditions. The contract they proposed required the acquisition of high-resolution bathymetric data in water depths of up to 300m over an 800km2 area off Thunder Bay, Ontario using Uncrewed Surface Vessel (USV) technology. Northern Lake Superior during late Autumn was deemed appropriate for testing the limits of this technology due to its harsh environment yet proximity to civilization should anything go wrong. IIC Technologies Inc and XOCEAN Ltd were the successful bidders to undertake the project. IIC is a hydrographic service provider with a 25-year history of providing hydrographic surveying, data processing, charting, consulting, and training services to hydrographic offices around the world. IIC provided in-country hydrographers, data processing and ground operations. XOCEAN is a technology company which uses USVs to provide turnkey data collection services to surveyors, companies, and agencies. XOCEAN was responsible for providing two XO-450 USVs, survey equipment as well as operators who monitored remotely from offices in Canada, the UK and Ireland.
3. Equipment
The two USVs used in this survey were XO-450 Uncrewed Surface Vessels which were built and operated by XOCEAN. The two units weigh 750kg each and have dimensions of 4.5m x 2.2m. They are roughly the size of a small car and are built with composite wave-piercing catamaran style hulls. The USVs are powered by a single cylinder diesel generator and a solar panel deck which provide power to an electric motor. The unit’s dual stern thrusters provide an operational speed of 3-4 knots. The USVs are very stable and boast the ability to survey up to sea state 5 on the Beaufort scale and survive sea states of 6. The units are equipped with 360-degree visual light cameras, AIS and a rotating thermal imaging camera. In addition, the USVs have active RADAR reflectors, navigation lights and a sound signaling device which allows them to be easily seen by other vessels in the area (XOCEAN, n.d.) (Figure 1). For this survey both units were equipped with a Kongsberg EM2040P Multi-Beam Echosounder System (MBES), Applanix Wave- master II Inertial Motion Unit (IMU) and Trimble GA830 Global Navigation Satellite System (GNSS) Antenna. Sound Velocity Profiles were collected using a Valeport Swift Sound Velocity Profiler (SVP) connected to an Auto-deploying winch. For surface water sound velocity comparisons an AML mini-SV was attached to the MBES system and provided live measurements to the operators. A stern view layout of equipment can be seen in Figure 2 and a top view can be seen in Figure 3.
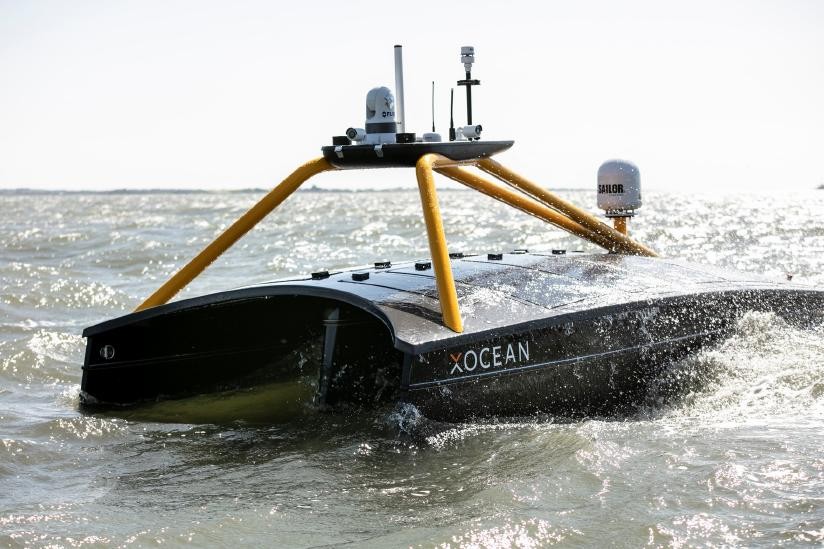
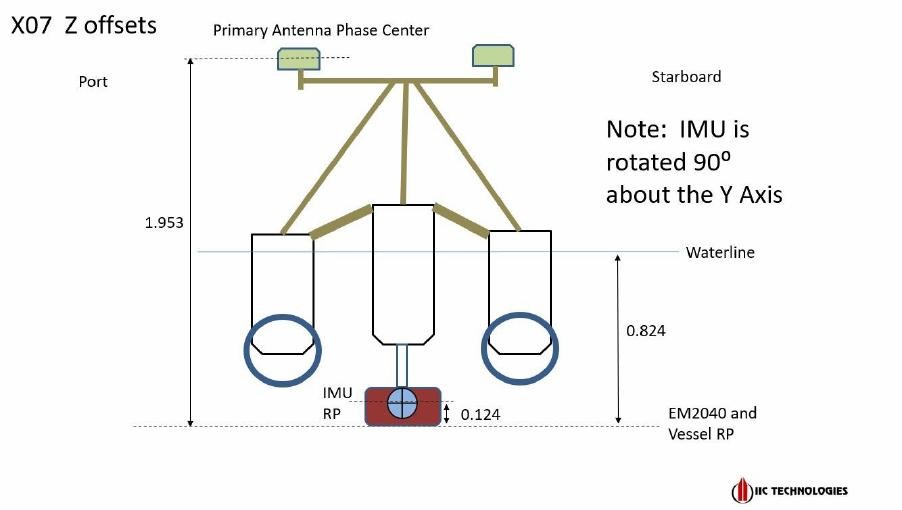
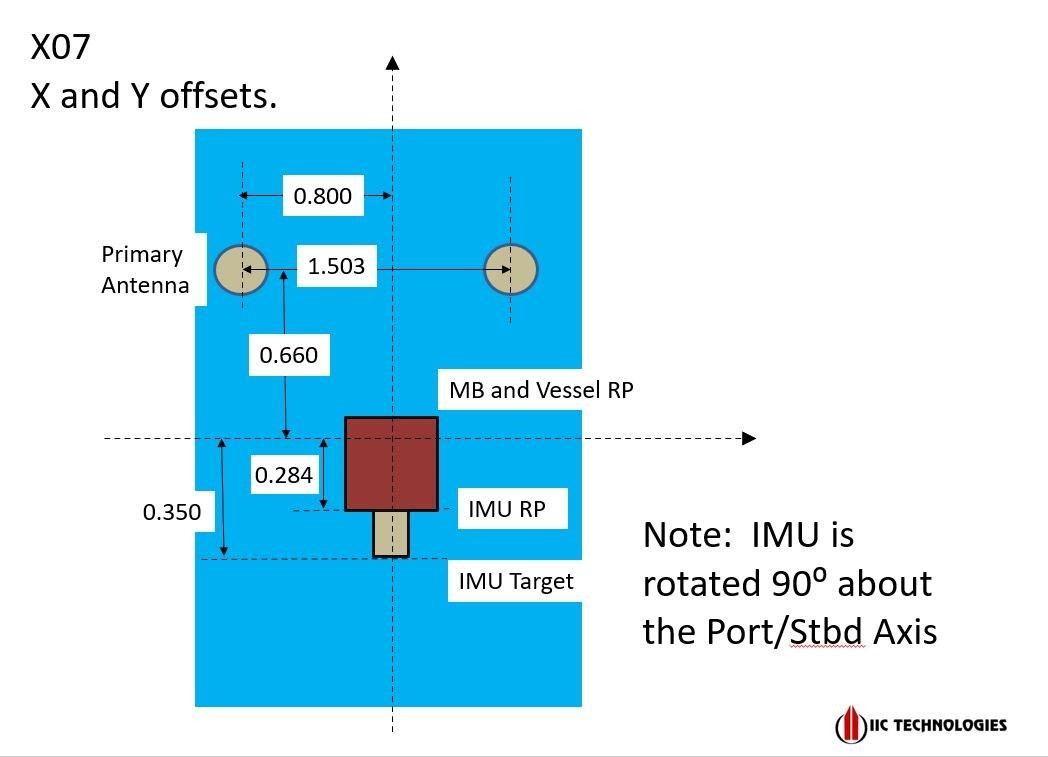
4. Uncrewed Piloting
XOCEANs USVs offer fully uncrewed ‘Over-The-Horizon’ operation using satellite communications. While following pre-programmed lines, the USV sends real time images and situational awareness data to XOCEAN’s Control Room where a team of qualified USV Pilots keep watch 24/7 and who, if required (i.e., for collision avoidance), can control the system manually. Otherwise, the system will operate autonomously following the preselected (or autoswath) survey lines. The USV will automatically adjust speeds and heading to run the given pattern. Survey lines were computed automatically using the QPS QINSy AutoSwath function where the survey line follows the outer edge of the previous line, with a user specified overlap percentage. For quality assurance, surveyors worked in shifts to monitor the MBES data feed remotely. Surveyors for this contract controlled the MBES using the Kongsberg K-Controller software and monitored the data through QINSy. This system was operated autonomously with USV pilot supervision for a period of approximately one week on each trip to the survey site before coming to shore for data download. This also provided opportunity for re-fueling and regular maintenance such as generator oil and impeller changes.
5. Conditions of Lake Superior
Those unfamiliar with the Great Lakes may question how the environment could simulate the operational conditions of the Arctic Ocean. For reference, Lake Superior is one of the largest bodies of freshwater on the planet and contains 10% of all freshwater on Earth (Minnesota Department of Natural Resources, 2014).The Great Lakes are known for their intense storms and November Gales which have taken the lives of sailors delivering materials between the various communities along the coast (Minnesota Historical Society, n.d.). Temperature tends to drop quickly in late autumn with Thunder Bay’s average monthly temperatures going from 6 to -11 degrees Celsius from October to December (Merkel, n.d.) Average water temperatures are also low changing from 10 to 4 degrees Celsius over the same period (Merkel, n.d.). Generally, ice begins to form in the lake around the end of November with the potential for rapid freezing in December. Lake Superior covers an area of over 82,879km2 with large swaths of open water and is the coldest of all the Great Lakes (Klock, 2002). During the fall and winter, winds are typically 10-15 knots greater than they are over land (Klock, 2002). The average observed sea state was 3 (As recorded in the Daily Progress Reports (DPRs)), while the maximum observed sea state was 6. The average observed wind speed was 25 knots (DPRs). It should be noted that this data only covers days when an USV was on the water to observe conditions. Thunder Bay is the largest community near the survey area and was roughly 23km from the edge of the survey block. With a population of 121,000, Thunder Bay is significantly larger than any community in Canada’s Arctic. It provided access to big box stores, mechanics and marine specialty stores which generally become harder to find further North. Having access to the amenities of a city helped ensure a smooth operation when working out technical issues (Figure 4).
6. Mobilization
Operations began in October with the offsite mobilization of the first USV in Lunenburg, Nova Scotia. Local IIC resources who were not impacted by the COVID19-imposed provincial travel restrictions met with XOCEAN personnel from their Canadian Office. Both teams practiced proper social distancing requirements while XOCEAN and IIC performed a dry run of actual operations. IIC personnel practiced safe launch, recovery, and local piloting of the USV (via joystick). In addition, IIC reviewed XOCEANS SOPs and discussed maintenance procedures such how to safely refuel the vessels, complete oil changes and ensure the unit is watertight (Figure 5).
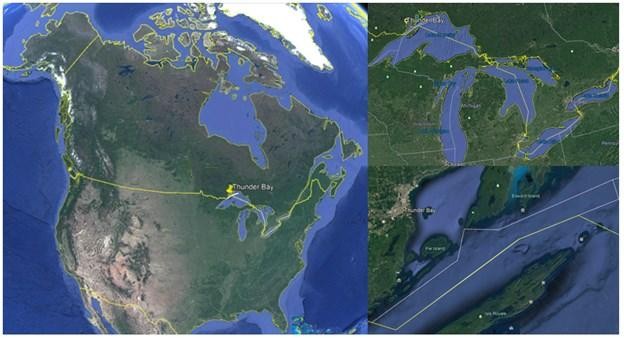
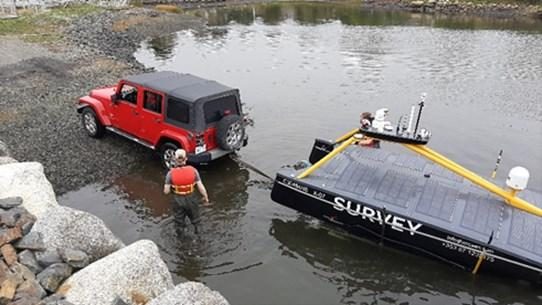
The USV was transported to Thunder Bay in a standard shipping container complete with all necessary tools, spare parts, manuals, and maintenance materials. Once in Thunder Bay, IIC contracted a local company (McKellar Marine) to assist with the unloading and launch. Due to the compact nature of the USVs, most of the mobilization was done offsite by technicians who have access to a full range of tools and a garage with space to work. This allowed for a quick turnaround time with the IIC Party Chief only needing to complete initial systems checks after unloading. These tests included pressurizing the hull to check for leaks, testing the launch and recovery of the auto winch and communications tests with XOCEAN personnel in Ireland. IIC had the USV in the water and running patch tests the day after the container arrived. The mobilization of a similar sized survey vessel by this means would prove more difficult in northern communities. Generally, mobilization is done from scratch when the vessel is alongside a wharf or on a trailer. Access to facilities such as garages would have to be planned well in advance and the simple failure to pack certain tools or spare parts could prove detrimental when sourcing replacements. Many surveyors can attest to their despair when dropping a small piece of their system or a tool off the dock with replacements days away (Figure 6).
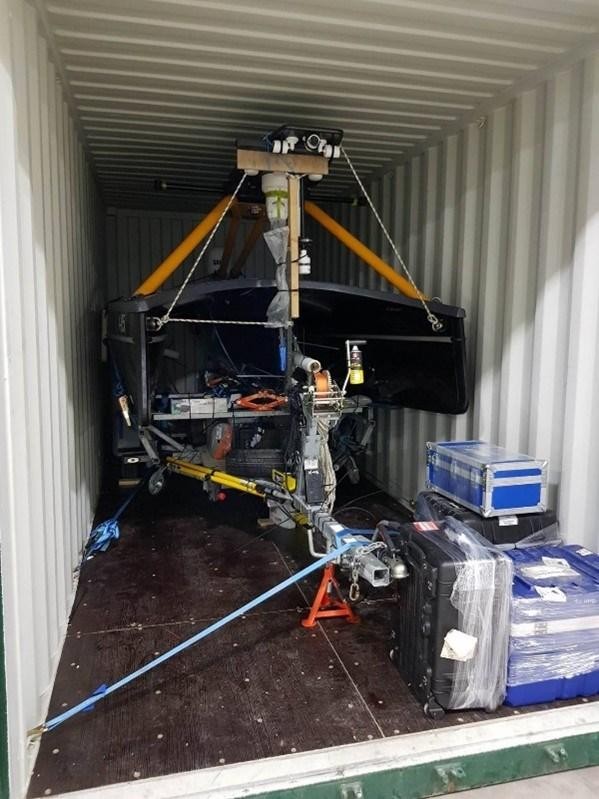
7. USV Survey Workflow
Regular survey operations began on October 13th, 2020. IIC utilized the crew of Thunder Bay Tug Services, who provided a chase boat and experienced crew to help guide the USV safely out of the harbour. IIC manually piloted the USV from the chase boat until it had cleared the break water. From there on XOCEAN pilots would assume control and navigate to the survey block (Figure 7). At that point, the USV would be set to automatically follow survey lines, with the pilots simply monitoring operations. A 50% overlap between adjacent lines was specified by CHS and this value was entered into the QINSy AutoSwath settings. The survey lines are no longer straight but follow the outer edge of the previous swath with a user defined smoothing factor. Using AutoSwath, data density, quality and efficiency are all easily controlled. The acquisition software automatically started logging when the USV reached the edge of the survey area. The USV then followed the AutoSwath created line until it reached the end of the survey area where it automatically stopped logging. A new line is then created by AutoSwath and automatically loaded into the autopilot driver which then steers the USV along it. When the edge of the survey area is reached, logging is started automatically, and the process continues. The data collection process is essentially autonomous with the surveyor just monitoring the quality of the data. The elimination of infill survey lines is one of the best reasons for using AutoSwath (Figure 8). Sound velocity profiles were taken at regular intervals by the USV, down to 200m. This was controlled by the USV Pilot. During regular operations, the USV would work for roughly a week before coming in for a data download, while also being refueled and serviced. The chase boat would meet the USV at the breakwater and IIC personnel would assume control. The vessel would then be loaded onto a cradle and pulled out of the water. IIC would perform regular maintenance such as refueling, oil changes and impeller changes. Data would be downloaded, backed up and the USV would be re-launched. While the USV was surveying, the IIC Party Chief would process data and report any issues or data gaps to XOCEAN operators. From there, data was sent to IIC data processors for finalization and quality control. Barring technical issues and poor weather conditions this workflow proved to be productive. The 24 hour a day operation allowed crews to take full advantage of good weather windows and a majority of data processing could be completed by field personnel.
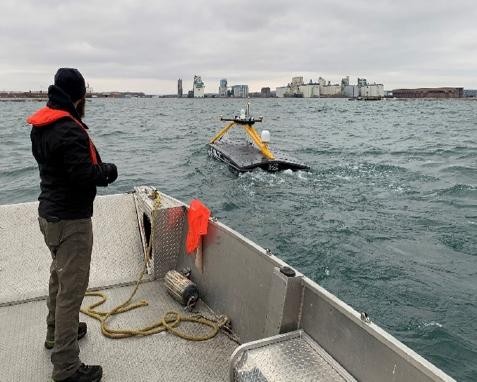
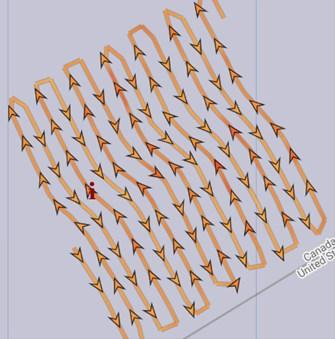
8. Operational Issues and Lessons Learned
One of the main goals of the project was to successfully survey the required area, which was accomplished on time and on budget. Another goal was to test this technology in Arctic-like conditions to uncover any operational issues and record lessons learned for future use in true Arctic conditions. This project presented excellent learning opportunities on what to expect and how to deal with operations in a northern environment.
- USV Transportation
The XO-450’s light weight design and relatively compact size allows it to easily be pushed around a garage floor and parking lot while loaded onto its cradle. When getting the USV ready for launch, two people were easily able to push it towards and line the unit up with the boat launch. From there straps were attached from the cradle to the back of a truck. Field personnel would push the USV down the ramp until gravity took over and the truck would guide the USV gently into the water. The large and robust tires of the cradle meant the unit had no issue getting over the many cracks and potholes common in asphalt that has been exposed to years of freezing and thawing cycles. Unfortunately, the second USV was not equipped in a similar way. The second cradle had thinner and solid plastic wheels designed for solid ground conditions that consistently got stuck in the many cracks. To help with this Thunder Bay Tug Services welded a custom trailer hitch that would allow the truck to push the USV over the potholes and down the ramp. However, the divots in the ramp made short work of these tires and moving the USV became near impossible. Replacement tires were quickly sourced from a local supplier and welded on. In addition to using the rugged model of cradle, for future projects a Transport Canada certified road trailer should be used to ensure a swift and safe transport and launch/recovery system if operating out of a coastal community. While it will not always be the case, operators should assume poor road conditions when operating in rural areas. That said, this finding would obviously be less applicable if operating from a mothership (Figure 9).
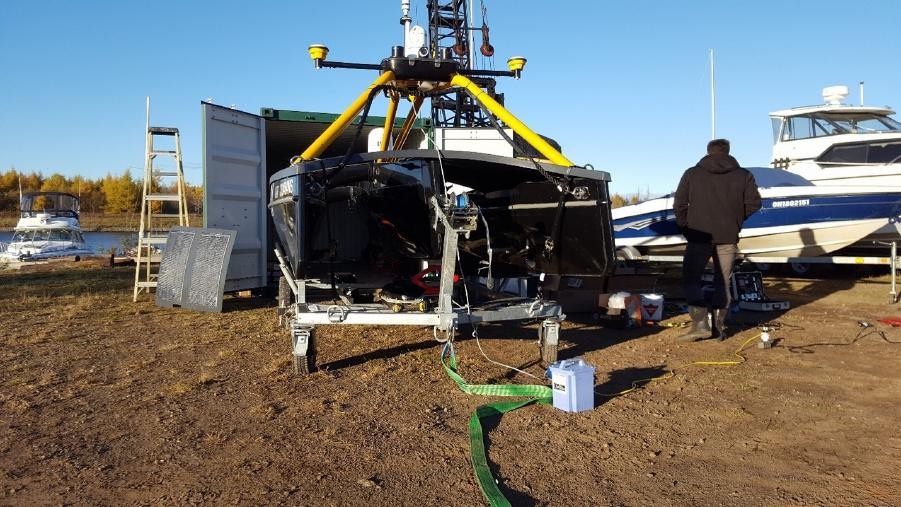
- Ice and Freezing Spray
High winds and low temperatures resulted in freezing spray early in the operation. Vessels in the region are often required to remove ice formations on a regular basis during winter months. These conditions become especially dangerous during long transits where it is common for ice to build up on just one side of the vessel. This build-up results in an uneven weight distribution and increased risk of capsizing. Operators were concerned that during long rounds of operation ice buildup would compromise the stability of the vessel. Fortunately, the low in the water design meant most of the vessel’s hull would be ice free as the water temperature of the lake helped to prevent freezing and the flat black deck helped to melt any ice that did form during daylight hours. Most ice formed on the gantry which is highly exposed to spray. However, the low surface area prevented large ice formations and did not dramatically change the weight distribution or impact the maneuverability of the vessel (Figure 10). There are several potential solutions to ice up issues when considering Arctic Operations where the USVs do not have quick access to a harbour and warm garage. For example, the crew from a mothership could perform regular de-icing operations using a hydrophobic spray similar to what is used on aircraft and wind turbines (Badische Anilin und Soda Fabrick, 2018). To limit the use of potentially harmful chemicals entering the marine environment, a small amount of spray could be used for cameras and navigational equipment while a hydrophobic paint/resin could be used for the general structure. New developments in hydrophobic technology are currently being implemented in the aviation industry but could prove beneficial in the marine sector as well (Badische Anilin und Soda Fabrick, 2018).
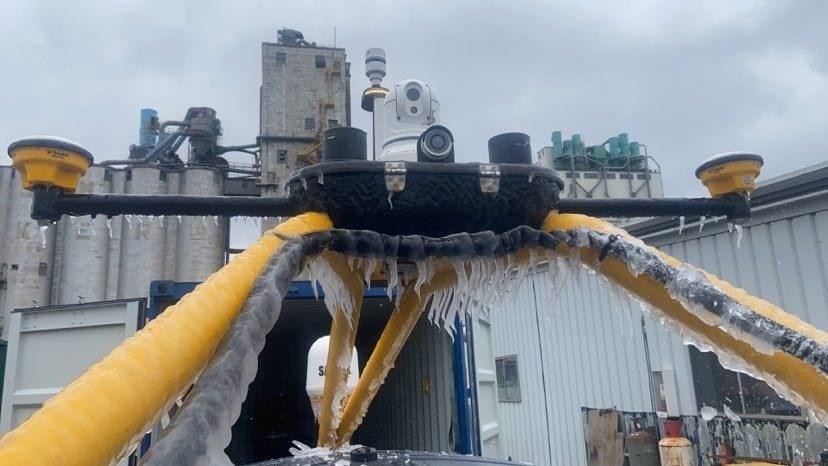
- Cold Considerations
Cold temperatures will prove a consistent issue when working in northern environments. It is often forgotten by people who do not live in these environments, that simple acts such as plugging your car in overnight and making sure things are completely drained of water are basic habits. Having a covered and heated area to perform maintenance tasks is essential to ensuring the longevity of equipment and for the safety of onsite personnel. When removing the USVs from the water it is impossible to ensure that they are completely dry. When performing regular maintenance or completing repairs outside or on the deck of a large vessel, it is likely that various hoses and water in the bilge will freeze and expand. This can result in internal leaks and blockages leading to equipment damage. In addition, it is essential to keep batteries charging and warm when not in operation to ensure a smooth generator start. IIC field staff ensured that the USVs were connected to shore power whenever they were out of the water for more than a few hours. In addition, space heaters were placed in all storage spaces and the crew would regularly sweep out the puddles of water that formed due to thawing. Failure to remove ice from the equipment and workspace creates a hazardous work environment.
- Frozen Air Intake
In November, a second USV arrived in Thunder Bay as per the project plan. This was launched and began survey operations shortly after arrival. After roughly a week a practical implication of a difference in design of the second USV’s air intake system was noted. Unlike the first USV, the second USV’s only source of air for the generator was up high in the gantry. This resulted in ice blocking the intake when the gantry froze over. The first USV had a secondary air intake lower down on the unit and closer to the water. Sections of the USVs that are closer to the water line proved less prone to freezing allowing a constant flow of fresh air. To replicate this in the second USV IIC installed two 1-inch skin fittings at the stern of the unit a few inches above the water line. Flex hose was run from there down into the bilge with a “goose neck” put in the middle of the hose. The “goose neck” helped to limit the entry of water that may be taken on by a chasing wave and gave a clear path to the bilge for any that did get in. Marine sealant was then used around the holes and deck plugs were used to perform a leak test. After the second USV successfully passed all systems check following the modifications it was relaunched and operated without issue until the end of the survey. The air intake, and other considerations for ice, freezing spray and cold should be closely examined for potential weak points, and these factors have resulted in an improved design of the XOCEAN USV air intake systems for future operations.
- Chase Boat Limitation
The CHS, IIC and XOCEAN all agreed to end the survey at the end of November once the mandatory survey area was done. The USV would have been able to operate past this date in the rapidly deteriorating conditions, navigating to more sheltered areas when required to avoid storms. However, conditions had become too dangerous for the Chase Boat to operate if it was required. If either USV experienced mechanical failure or began to take on water, no one would be able to render aid in a timely manner. All appropriately licensed and equipped vessels including the Canadian Coast Guard had ended operations for the season. Furthermore, boat launches had begun to freeze over meaning that launch and recovery would soon become impossible (Figure 11). The limiting factor of a Chase Boat (if required) needs to be considered when working in the Arctic. This factor could be reduced by using a mothership for launch and recovery rather than working out of a port. A larger vessel equipped with a Launch And Recovery System (LARS) for the USVs would be better suited to handle the conditions and allow for a faster and more safe recovery. As seen in Peyton 1992, the use of a recovery system specifically designed for launch and recovery of USVs was crucial for safe operations in the harsh environments of Northern Newfoundland. (Peyton 1992)
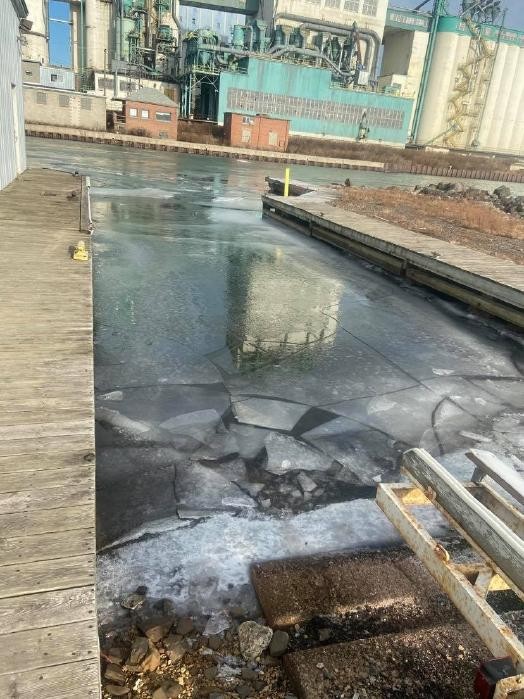
Operational Successes
Regardless of the obstacles overcome by the team, the uncovering of which was a major reason for the project in the first place, there were many operational benefits of USV technology that should be celebrated.
Safety
While most of the world was locked down and operations were halted, the remote nature of this technology allowed for a team of skilled personnel to safely operate and complete a contract with minimal contact between each other and the local community. Furthermore, the USV allowed for continuous 24/7 operations in conditions that would be considered too dangerous for a manned vessel. By utilizing remotely operated technology companies can dramatically limit the number of people being brought into the area, and greatly reduce the need for resources on the water.
Support of Local Communities
This operation would not have been successful if not for the support of local experts and businesses. The crew of Thunder Bay Tug Services provided a chase boat, crew, tools, repairs, space and local advice on conditions, weather patterns and businesses through which replacement parts and materials could be obtained. Mckellar Marine provided world class marine skills at the site, including providing an experienced diesel mechanic. Utilizing local crews and resources when possible benefits the economies of remote communities and provides operators with valuable local knowledge.
Environmental Considerations
The XOCEAN USVs also provide the benefits of a low Carbon Footprint, which is especially important in an area as sensitive as the Arctic. The XO-450 has 0.1% of CO2 emissions of a conventional vessel (XOCEAN, n.d.).The USV also provides an acoustically quiet platform, which generally reduces noise for marine life during survey operations, and makes it well suited for other applications such as fish stock surveys.
Multi-Sensor Capability
The Arctic Environment needs more than pure bathymetric data. The need for broader marine-based science data has also increased in the area as it undergoes a fundamental change and becomes more accessible. Those in charge of managing these coastal areas will need data to tackle the challenges of the future. The latest autonomous vessels can operate a multitude of sensors collecting weather data, water quality and even seabed seismometers for early earthquake warning systems (Open Ocean Robotics, n.d.). Taking advantage of uncrewed and autonomous technology coastal managers can combine bathymetric and environmental data. This would assist in the creation of an up-to-date marine geospatial infrastructure which will aid in managing the region (Hains, 2020).
USV Performance Improvements
One key goal of the project was to enable the team to trial real world Arctic-like conditions, and then identify areas for future improvement. XOCEAN has already incorporated improvements into future systems based on the experience which are now undergoing sea trials. This includes the use of redundant generators to decrease their reliance on local chase boats, a double aluminum hull to increase endurance in icy environments, and improvements to the air intake system. Furthermore, a LARS for operations from a mothership is available to allow the XO-450 USVs to be safely lifted and housed on a vessel.
9. Conclusion
This highly collaborative and flexible partnership proved invaluable for the successful completion of this project. The ability for foreign crews to monitor remotely in conjunction with a small local ground crew made for an efficient acquisition program and allowed the team to overcome any problem that came their way safely and in compliance with COVID 19 restrictions. Based on this experience, IIC considers the use of USV technology a powerful force multiplier for future Arctic Surveys. A survey vessel housing crew and materials, leveraging multiple USVs, would dramatically increase efficiency, which is especially important for a region with a short operating season. Outside of Arctic operations the benefits of this technology in a world locked down by a pandemic, or in other situations where a traditional survey is not suitable, cannot be overstated. The use of remotely operated technology coupled with IIC’s global presence and belief in utilizing local resources will allow for rapid mobilization and operations with minimal onsite resource requirements. Many lessons were learned on the challenges of operating in northern environments and adaptations for the technology are already in the works. IIC and XOCEAN look forward to continuing their partnership and growing on what was learned for future operations in the Arctic region.
- IIC Technologies Inc; ; Ruairidh MacKenzie; Rory.Mackenzie@iictechnologies.com
- XOCEAN Limited; Duncan Mallace; Duncan.Mallace@xocean.com
- Canadian Hydrographic Service (CHS); Dave Bazowsky; Dave.Bazowsky@dfo-mpo.gc.ca