Agile Underwater Platform with Integrated Sensors for Environmental and Visual Applications
Abstract
The Fraunhofer “Smart Ocean Technologies” (SOT) research team extends its range of services towards underwater technology by developing new internal infrastructure. To test sensor technology and materials, empirical underwater data is required to evaluate new technology within realistic conditions. Various external factors like swell, wind, and the underwater environment itself complicate stable framework conditions during the measurements. For this purpose, a test platform called MiniLab was developed which can be extended by modules with respect to common interfaces. It serves as a base frame for internal as well as external projects. The MiniLab consists of an underwater unit and an on-ground unit. Both are connected via a hybrid underwater cable. In addition to the environmental conditions, camera live streams can be transmitted. The MiniLab service platform is currently being used in the Warnow River and in the Digital Ocean Lab (DOL) in the Baltic Sea. However, it is available for observations in other waters (Fraunhofer, 2021a).
1. Introduction
The multidisciplinary Fraunhofer research group Smart Ocean Technologies (SOT) is developing pioneering marine technology and new solutions for the sustainable use of the oceans. As a cross-institutional research network in underwater technology, it is embedded in the context of the Ocean Technology Campus Rostock and operate a nearby underwater testing ground in the Baltic Sea, the Digital Ocean Lab (Fraunhofer, 2021b).
The SOT group is working in various underwater research projects. Within multiple research projects it is advantageous or even necessary to track underwater conditions. The MiniLab aims to meet this requirement. With MiniLab as a tool, the SOT group is able to do tests under realistic conditions without a high level of organizational effort. Due to the development of MiniLab, the group gained a lot of experience. This experience ranges from the definition of requirements through conception, construction plans, designs and procurement to the construction and testing of watertight equipment.
The Project MiniLab started in 2021 from scratch and will be finished by the end of July 2023. The overall project is divided into three parts: 1. Basic system, 2. Radio-based communication and 3. Mobility of the system. This paper describes the basic system regarding overall requirements, hardware and software architecture, and future steps for the radio-based communication. Furthermore, our first practical tests are shown, and general application examples are given.
2. Requirements
The basic idea of the MiniLab project is a platform for testing and development of new features, devices, or materials underwater. To ensure a robust architecture the platform needs to fit several high-level requirements as indicated in Table 1.
The following hardware and software architecture are derived from these high-level requirements.
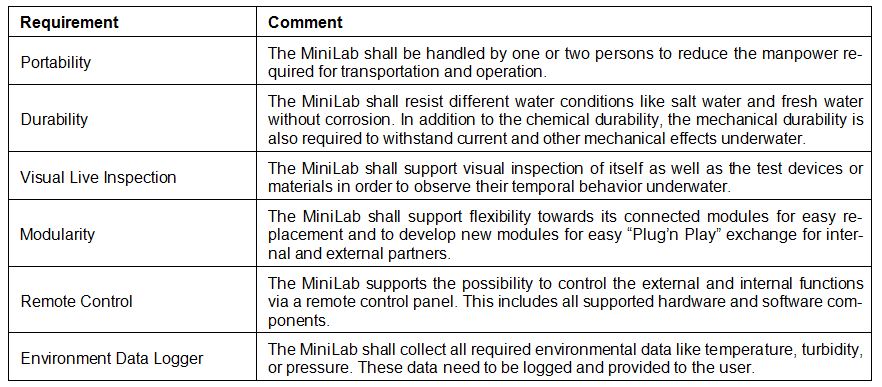
3. Hardware of the MiniLab System
Portability, durability within the water environment and modularity are important for the MiniLab system. The system includes two units: an on-ground unit (Figure 1) and the underwater unit (Figure 3). In order to ensure the portability, the on-ground unit is built inside a case. Within this case a power converter transforms 220V (AC) power supply into 48V (DC), which forms the power supply for the underwater station. The unit on ground level contains an external power supply for devices (1), two switches to put both stations into operation (2 and 3), the connector for the cable that powers the underwater station (4), a 220V power supply for the on-ground station itself (5) and multiple options to connect to the MiniLab network via Ethernet (6).
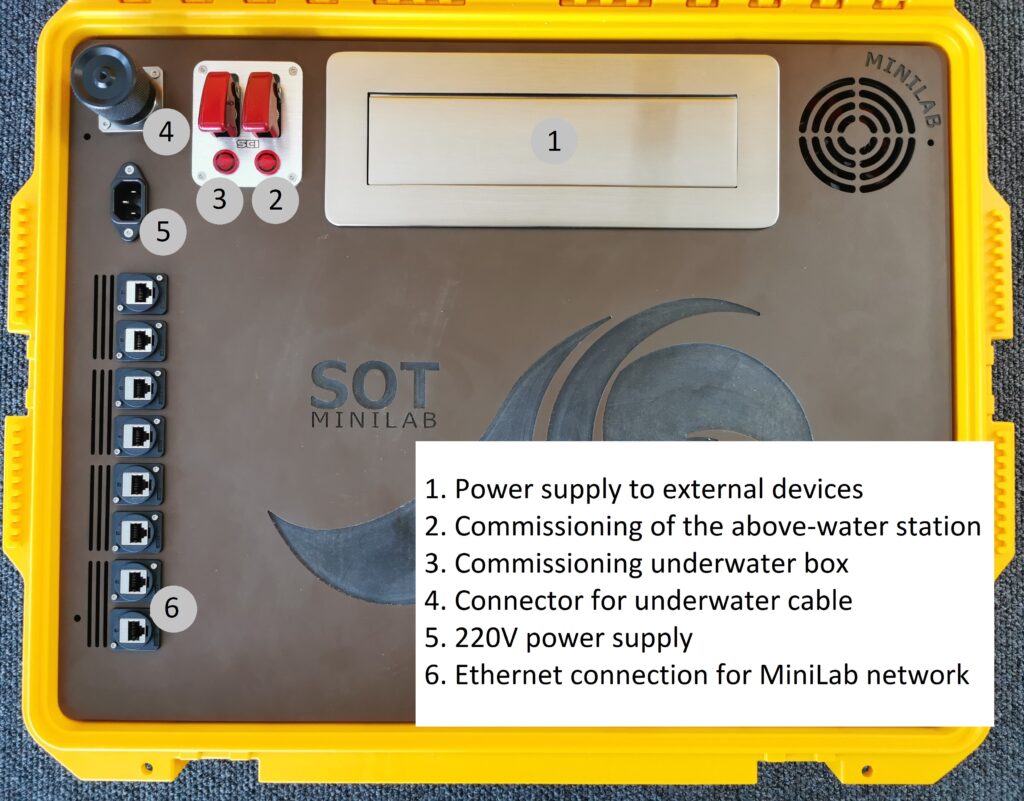
The heart of the underwater unit (Figure 2, top left corner) is the Raspberry Pi. It allows the communication with the sensors and cameras that are also installed on the underwater unit.
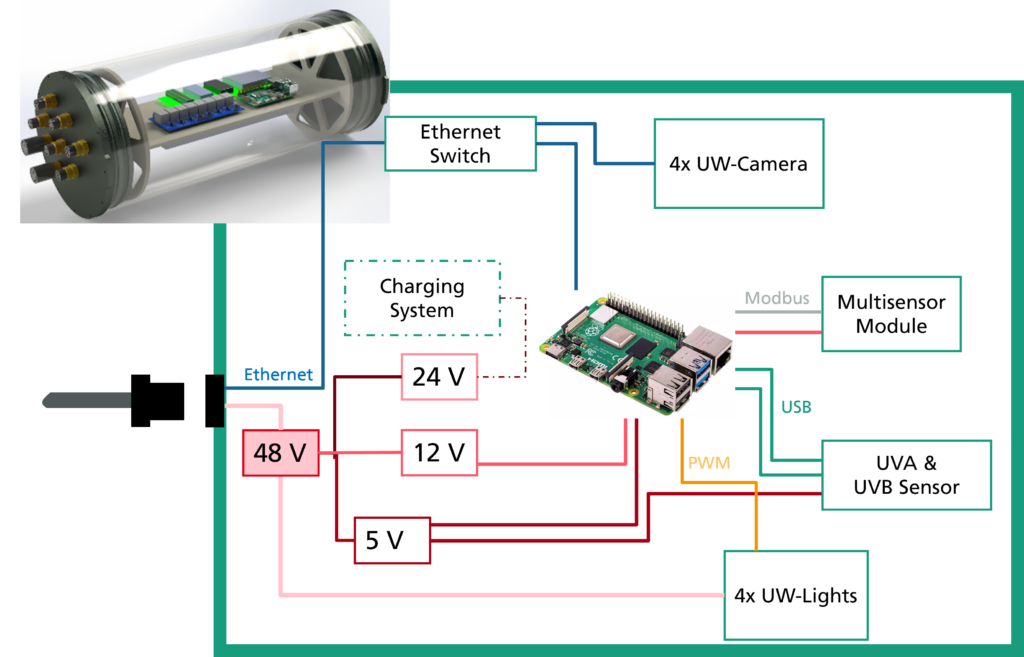
The basic structure of the station can be seen in Figure 2. So far it consists of four underwater cameras, a multi-sensor module, two UV sensors and four underwater lights. A multi-sensor module is used to measure pressure, temperature and conductivity, the pH value, dissolved oxygen, water turbidity and chlorophyll. The module can be expanded to include nitrate/ammonium, chloride, bromide and carbon dioxide values. The UV sensors collect data for UVA and UVB radiation. For visual checks and documentation, four underwater cameras and a dimmable light system are available, which can be freely placed and aligned in the underwater unit.
Since the Raspberry Pi is capable of various communication protocols the hardware can be extended to specific needs. Apart from the initial 48V power supply coming from the surface the underwater devices can be powered with 24V, 12V and 5V as well. The conversion to 24V will be used in the future for a charging system. The 12V power supply is used by the multi-sensor module and the 5V power supply is used for the Raspberry Pi and the UV sensors. Only the underwater lights are using the full 48V as can be seen in Figure 2 as well.
Therefore, the underwater station connects all components into a MiniLab network, making the data of all sensors available to the surface station via ethernet connection.
The underwater components are held by a frame made of stainless steel with an edge length of 68cm × 68cm and a height of approximately 65cm (Figure 3). A modular and stable design of MiniLab also ensures flexible adaptation to individual applications. The system can be lowered to the river or sea ground. The main underwater unit is connected to the surface unit via a 40m long, hybrid, waterproof and Kevlar-reinforced polyurethane underwater cable. Six copper wires transmit the electrical power. The communication runs over two fiber optic cables to ensure maximum bandwidth.
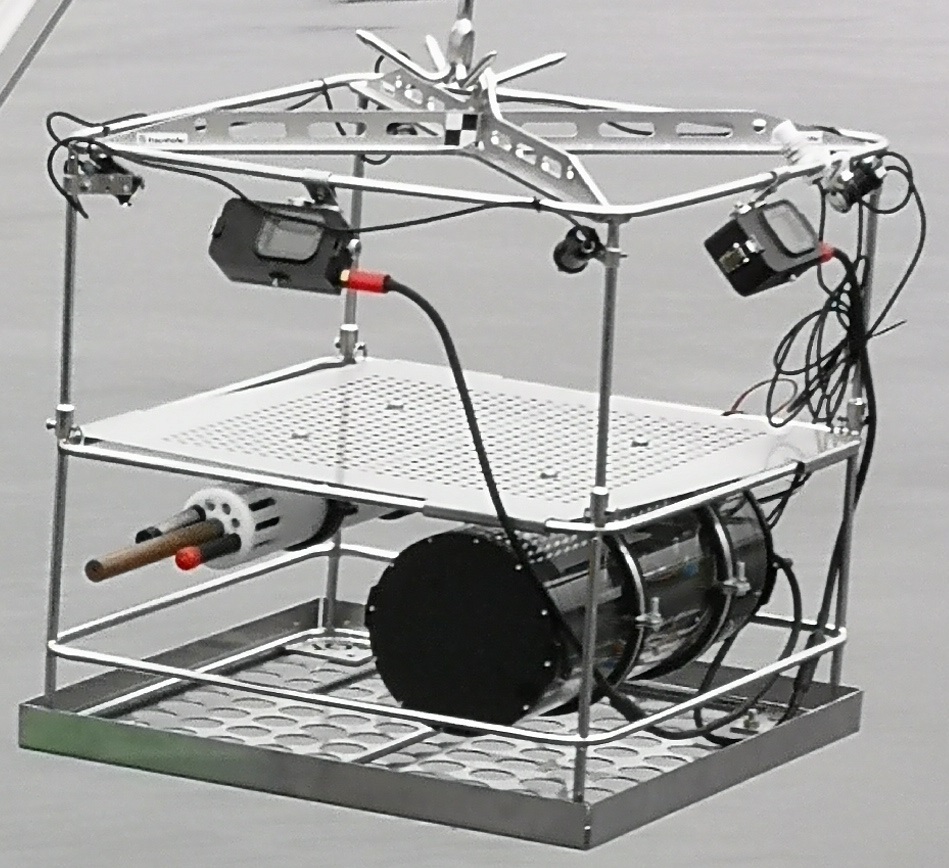
4. Software MiniLab
Like the hardware design and architecture, the software design and architecture follow the high-level system requirements. The internal software structure can be divided into services, database, and backend to ensure the given requirements of modularity and robustness.
The main node of the system is the database for the data exchange between the services and the backend. Each service is designed to fulfill a single task and can run as stand-alone application to collect data from sensors or other devices under test. The single services support different kind of data types like configuration data and parameter as well as measurement data. Configuration data are set once a service is started and cannot be changed during the runtime. To allow users to change the operation mode of the connected device or service, the service supports parameter settings. Independent from these data are the measurement data which are collected from the connected devices. All kinds of data types are periodically stored in the database (Figure 4).
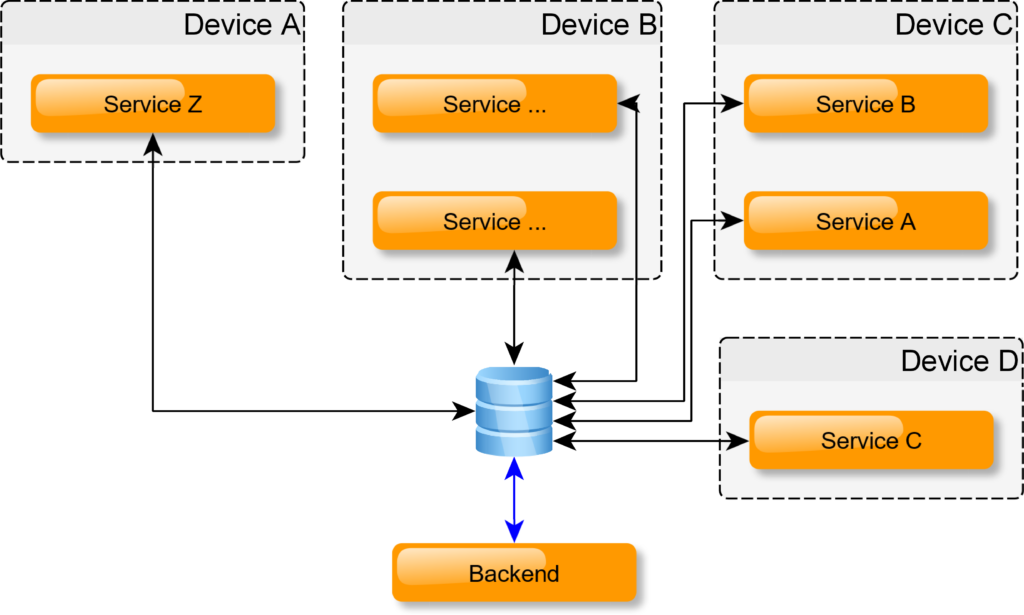
The database itself is the time series database “InfluxDB” which provides a rest API interface for the data exchange. This rest API is not only used by the services, but it is also used by the backend. The backend allows the user to get remote access towards all connected services. It handles all kinds of information and provides a rest API as well. For the user on the other side, it is only a web interface to control the whole MiniLab system and observe the ensemble of information from the services.
5. Practical Tests
The MiniLab system was officially presented at the beginning of June 2022 in the Rostock Cargo and Fishery Port (Figures 5 and 6). The left picture shows how the system can be lowered into water with the help of a crane. The right picture shows the surface case and the communication with the system via a personal computer.
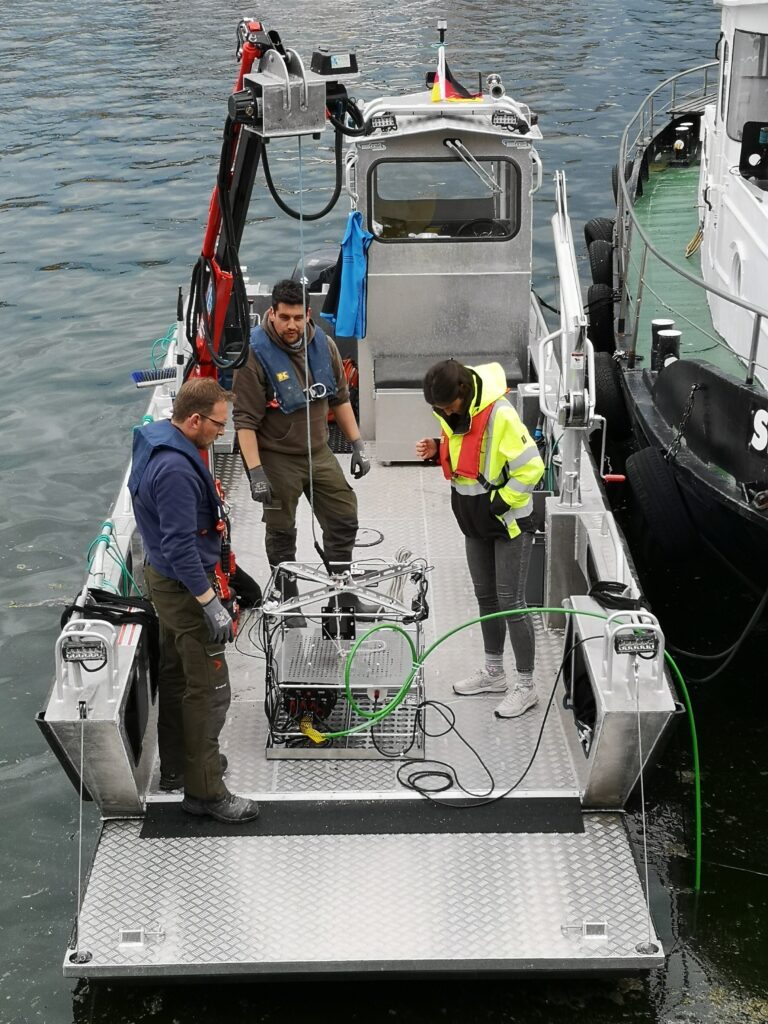
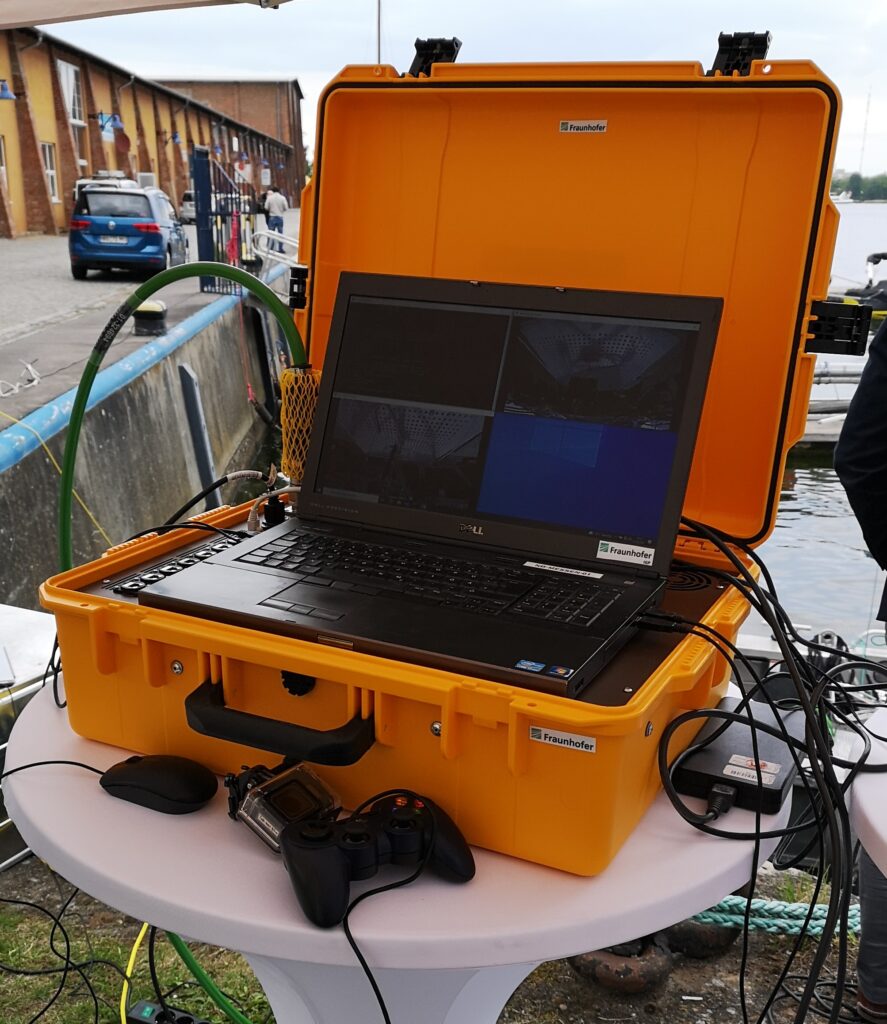
Another field test including more functionalities of the MiniLab system was carried out at the end of September 2022 in the Warnow River (Figures 7 and 8). All sensors and the control software were successfully tested. Figure 7 shows the MiniLab underwater unit. Figure 8 shows a photo of the underwater camera live stream. The camera is faced towards the surface for materials or specimens to be observed and tested within the MiniLab. For the field test, calcareous tubeworms were used as exemplary test material.
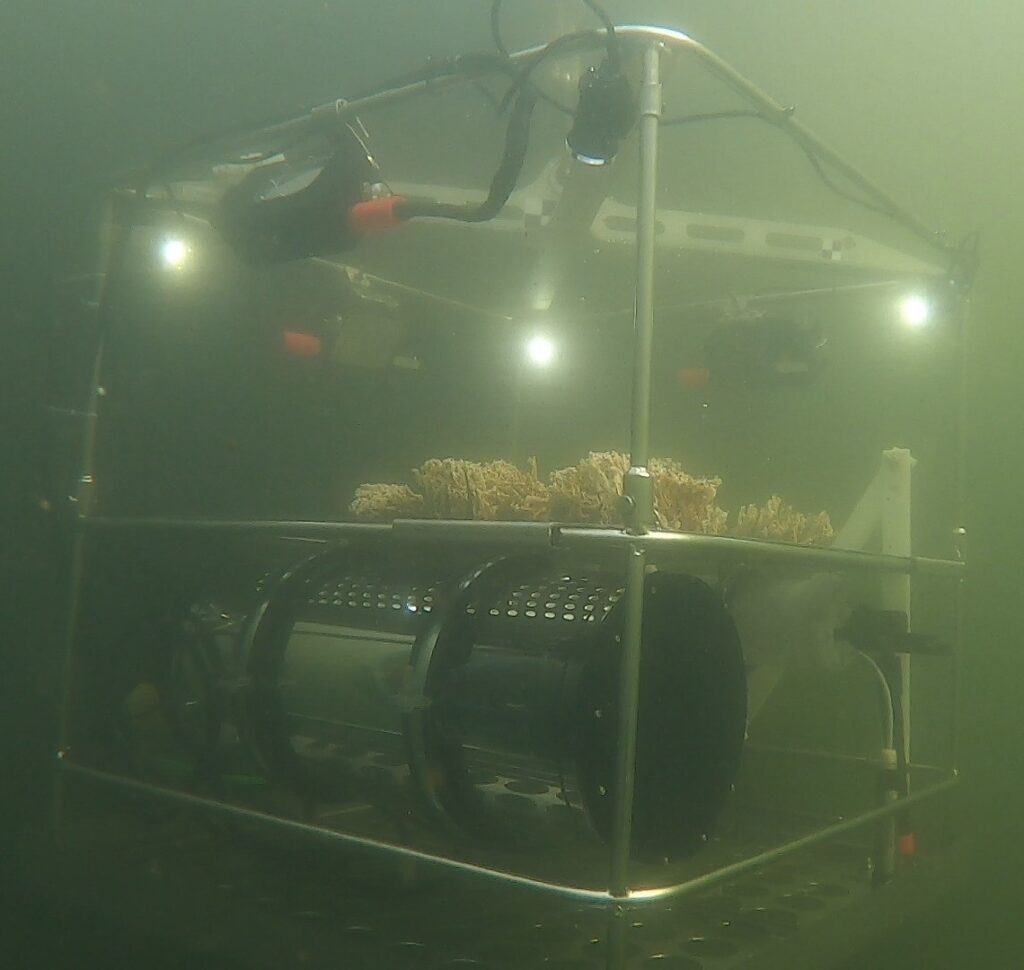
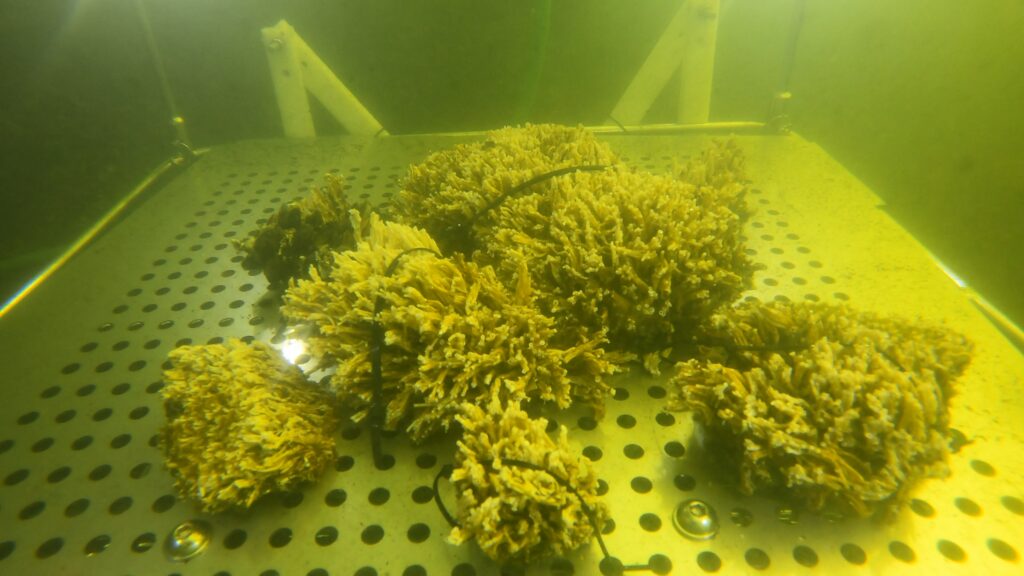
Figure 9 shows the interface of the website. On the left there are multiple services shown that run during operation. The services include sensor communication as well as camera streaming. Within the website it is possible to access data or influence a service. The service for the underwater lights for example enables direct control of the PWM (pulse width modulation) value sent to the lights. This allows dimming the lights directly from the website. The data can be shown in different diagrams for multiple time periods. In Figure 9 on the right one can see a temperature graph showing the temperature drop when lowering the MiniLab into the water.

6. Application Scenarios
MiniLab was developed for different purposes. From the technological point of view, the platform is intended as a carrier for various sensors. Due to standardized connections for plugs and power supply any kind of sensor technology can easily be tested in MiniLab. The only limit is the size of the frame used for MiniLab.
From the research perspective, MiniLab serves as an observation and data collection platform. By using a cage system inside the frame, it is possible to perform material tests and other experiments while recording environmental parameters. This allows, e.g., studies on anti-fouling properties of different sample materials, on weathering of plastics, but also the observation of biodiversity of existing ecosystems nearby. The last-mentioned scenario is especially of relevance for the construction of artificial reefs for renaturation after the dismantling of offshore facilities or in the course of rebuilding otherwise destroyed ecosystems.
As one example, the system platform MiniLab could be used for a systematic recording of the growth of the Australian tubeworm ficopomatus enigmaticus (see Figure 8). This worm as an invasive species in the Warnow River was observed for the first time in 2016 during a usual survey. After an absence in the years 2017 and 2018, the worm reappeared in 2019 (Hille et al., 2021). As a generalist, it is very adaptable and robust to different conditions regarding salinity, water temperature and pH-value of the water. However, the current state of research on it comprises only single studies of very limited duration. Therefore, MiniLab would be an ideal platform with its automatic recording of environmental parameters at regular intervals over months using suitable sensor technology to characterize the growth of the Australian tubeworm. In this case, advanced image acquisition tools (e.g., UW image enhancement and analysis based on machine learning algorithms) will also be embedded in the system.
7. Future Work: Radio-based Communication
In the next project stage, the MiniLab should be expanded so that measurements can be carried out over a longer period of time, e.g. in the Baltic Sea, using radio-based communication (Figure 10). This will lead to an increased demand on the power supply and to a challenging design of the communication system. Therefore, a buoy is planned to be integrated into the existing process chain. The underwater cable will be installed between the buoy and the underwater unit. Therefore, the communication will be facilitated with the help of an LTE (Long Term Evolution) router and the power supply will be provided by a battery system. The main part of this project will be the battery configuration and setup.
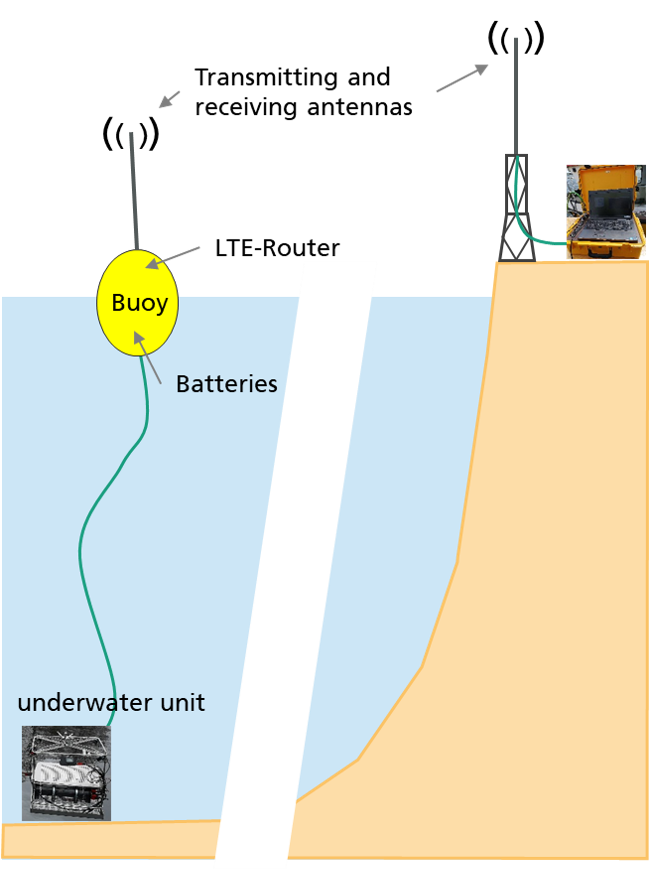
8. Conclusion
The SOT group successfully installed the MiniLab to generate and process data from various sensors underwater. The developing process of the platform has strengthened the SOT group’s capabilities in the field of underwater technology and resulted in an extremely useful test bed for further experiments. The system can be operated by only two people and is very versatile in its possible applications. All set requirements have been met. The user interface is currently a first draft and will be expanded in the future. However, the MiniLab is ready to use for external partners or for internal projects that require an easy-accessible, modular underwater platform. Operations in various lakes, rivers and coastal waters of the sea are conceivable. Furthermore, all components of the underwater unit are modular and can be arranged at other frames or boat designs. It is also possible to integrate additional hardware and manage power supply and communication via MiniLab.
9. Outlook
With the help of radio-based communication, MiniLab can also be used away from the shore and over several days. This feature enhancement is currently being worked on.
In the future a mobile control station is intended to make the operation of the MiniLab easier and more convenient at different locations and in different periods of the year. A trailer has to be modified for this purpose. An operator should be able to control the MiniLab from there. The trailer would also be used as a way of transporting the units of the MiniLab. In addition, a swimming launch and recovery system should be very helpful for heavy weight operations.
10. Acknowledgments
This work was funded by the Federal Ministry of Education and Research and the Ministry of Education, Science and Culture Mecklenburg-West Pomerania.
11. References
Fraunhofer (2021a). MiniLab – the agile underwater platform project. https://www.smart-ocean.fraunhofer.de/en/projects/mini-lab.html, viewed 02.10.2022.
Fraunhofer (2021b). Smart Ocean Technologies SOT. https://www.smart-ocean.fraunhofer.de/en.html, viewed 02.10.2022.
Hille, S., Kunz, F., Markfort, G., Ritzenhofen, L., Zettler, M. (2021). First record of mass occurrence of the tubeworm Ficopomatus enigmaticus (Fauvel, 1923) (Serpulidae: Polychaeta) in coastal waters of the Baltic Sea. In: BIR 10 (4), S. 859–868. DOI: 10.3391/bir.2021.10.4.10.